Preparation of cloth |
A cloth to be printed is boiled for removal of impurities and bleached to enable dye and medicinal agents to penetrate into the cloth easily.
|
Stock paste |
A pasting agent is mixed with water and heated while being stirred to produce stock paste. In days of old, the stock paste was made from starch of rice. |
Paste for printing |
The stock paste is mixed with a concentrated solution of dye and agents for printing, and stirred while adding water to control viscosity. The viscosity is important for dyeing of sharply defined patterns. |
Printing |
Printing is the procedure in which paste is placed on the pattern area using a mold with a fixed thickness. In this procedure, it is important to prevent the paste sticking to other areas. This enables clear patterns to be created on the cloth. In hand screen printing, the mold is moved by an artisan, while in machine printing, such as roller printing and automatic flat screen printing, the cloth is moved.
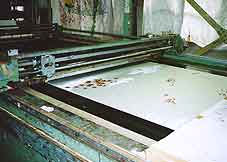
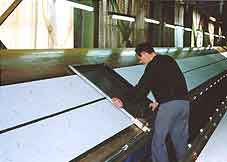 |
Drying |
Since dye may seep out of patterns upon fixing if printed areas of the cloth contain moisture, the cloth must be dried. The printing stand, which is in direct contact with the cloth, and drying cylinder are heated by steam from a boiler to dry the cloth.
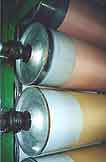 |
Fixing |
Dye is transferred to the cloth when steamed at high temperature and fixed to fibers. Pigment is fixed to fibers by drying and heat treatment at a high temperature. |
Washing with water
Soaping |
Washing with water and soaping (washing with detergent) are performed to remove excess dye, agent, and paste. In the past, cloths were placed in a river, instead of this procedure. |
Drying
Fabric inspection
Finishing |
The cloth is dried, inspected for uneven coloring, and finished (tentering, pasting, etc.). |